Albas cashmere from Ordos Plateau, Inner Mongolia, which is naturally unique.
By virtue of the exquisite craftsmanship.
Weaving the delicate beauty of warmth.
The warmth from nature and craftsmanship.
Dedicated to every love of luxury cashmere clothing, love of life.
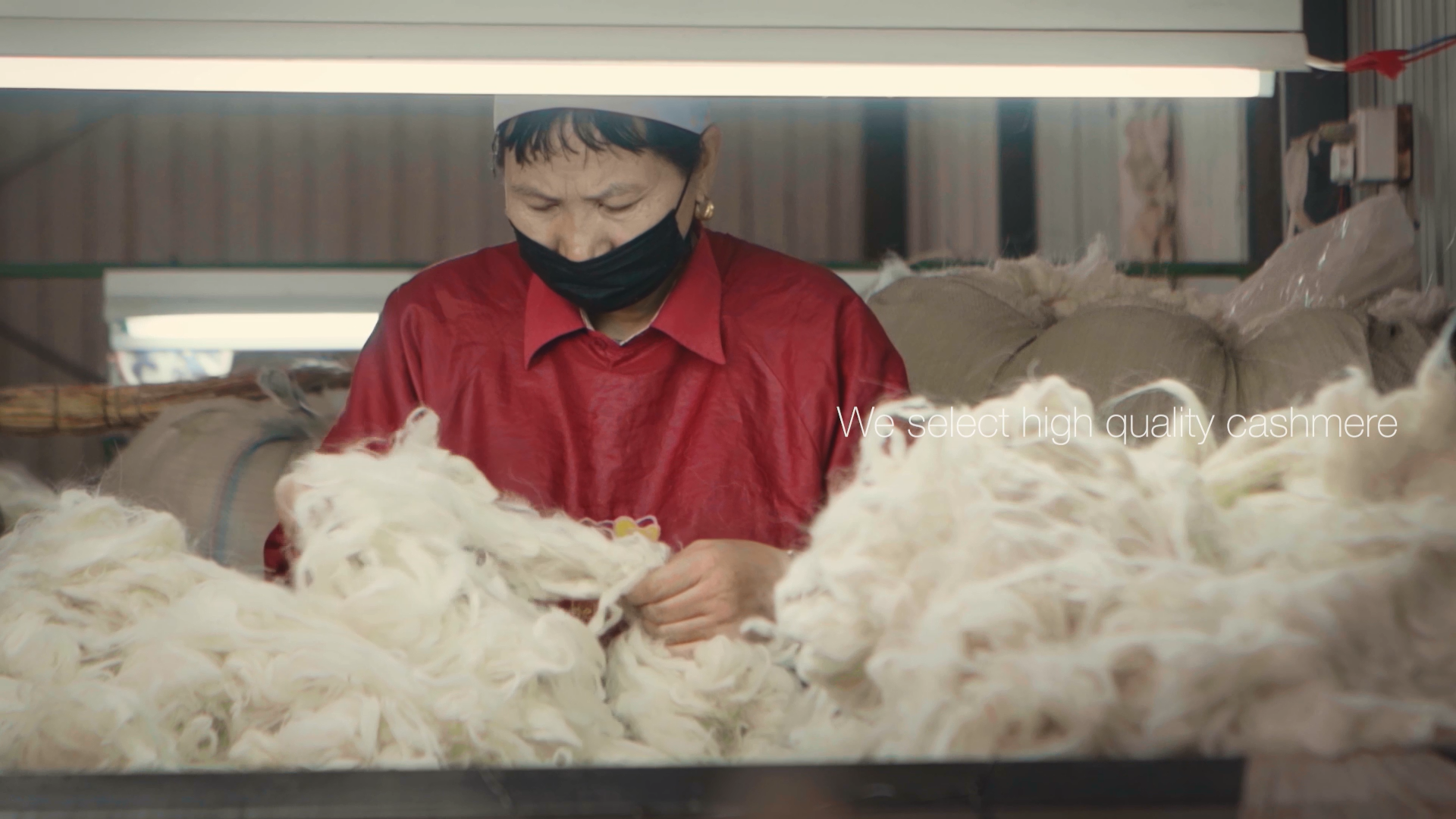
01
Handpicked Preliminary Selection
The raw cashmere combed from goats must first undergo the removal of impurities such as grass thorns, paint, discoloured fibres, and synthetic materials from nylon bags. This process cannot be handled by machines and serves as the first crucial line of defence in quality control. After being meticulously handpicked and sorted, the raw cashmere transforms into material that is “light as a cloud, white as snow, and soft as silk.”
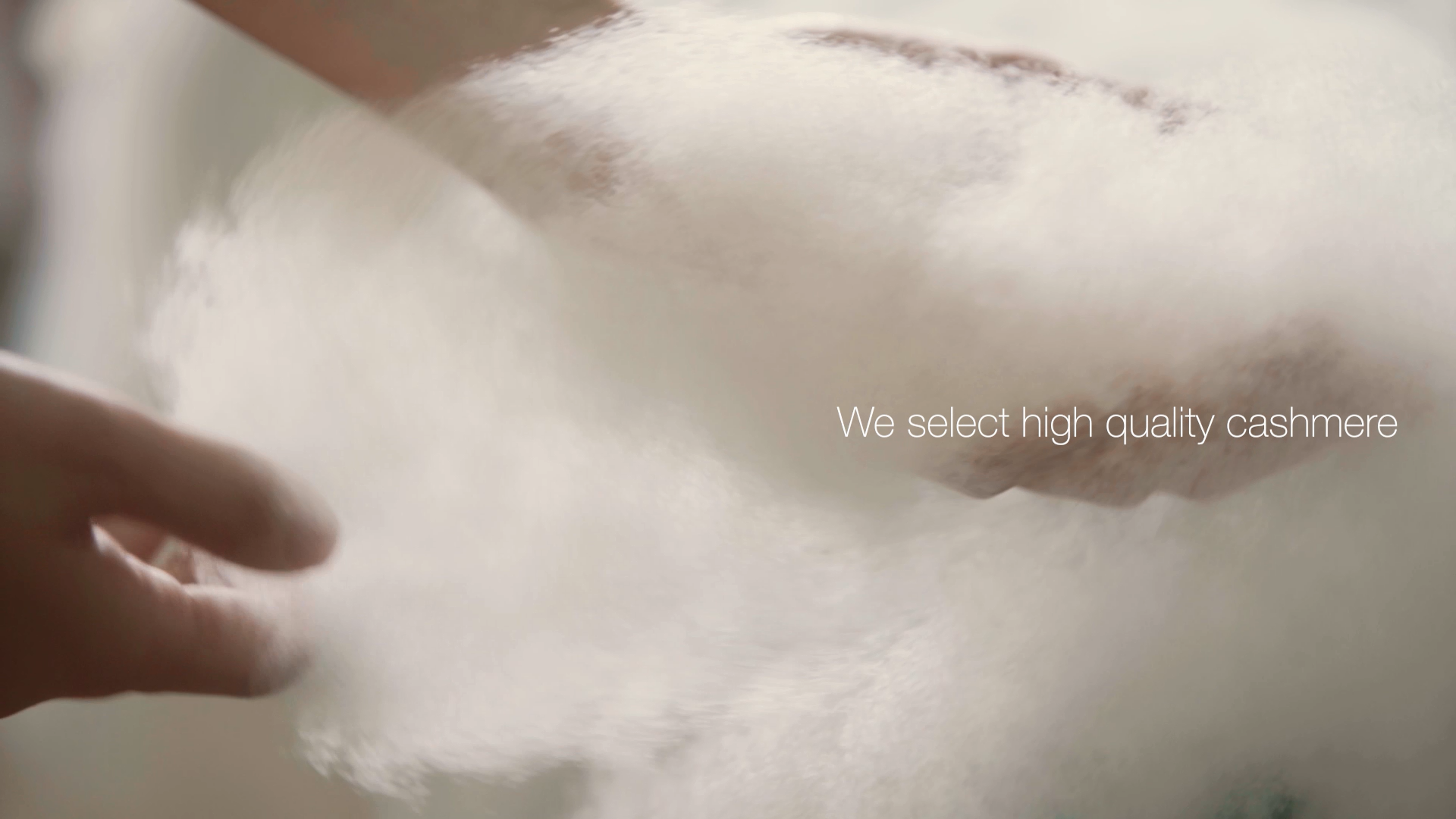
02
Combing
Once the raw cashmere has been thoroughly cleaned, it undergoes machine combing to completely remove fine wool and other impurities. The combing process must be repeated multiple times for the cashmere fibres to reveal their naturally pure quality. It typically requires at least seven or eight rounds of combing to achieve cashmere that is as light and fluffy as a cloud. While monitoring the machine’s operation, the master also checks whether the cashmere in the combing box is too dry. Lightly misting the cashmere with water helps prevent fibre damage, and this judgement is based on accumulated experience. Combing is the key to ensuring pure cashmere.
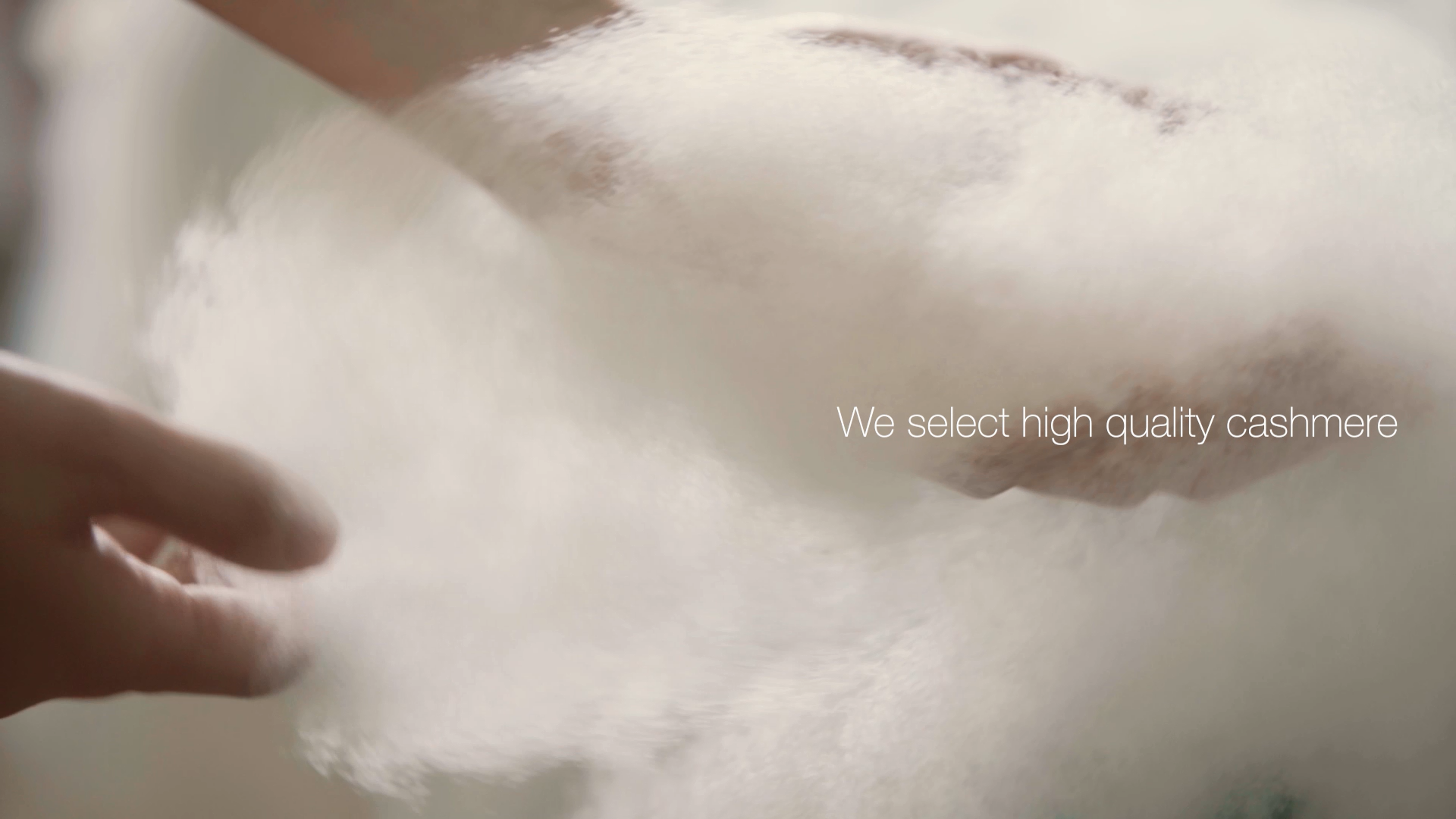
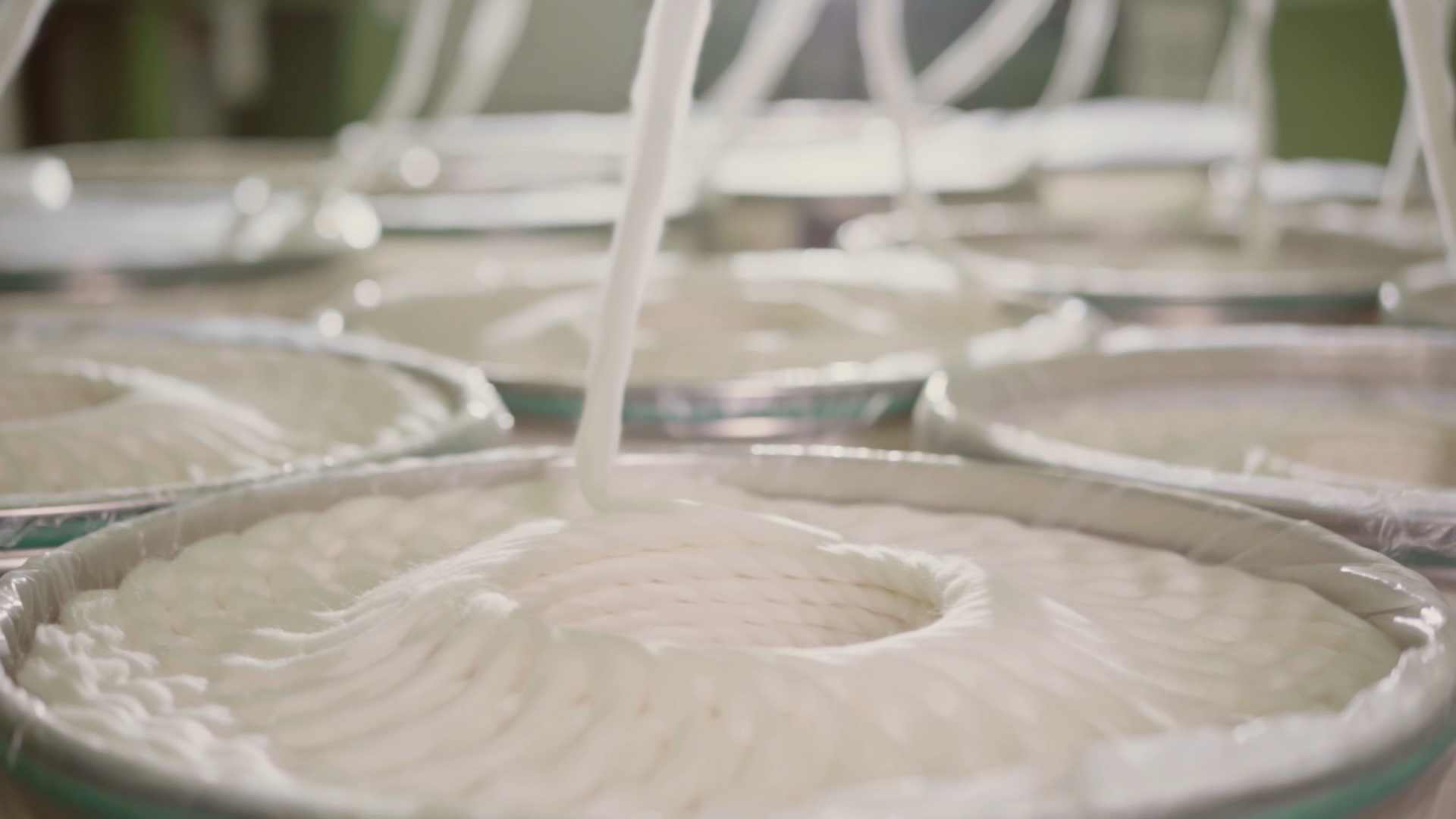
03
Slivering
Slivering is the process of preparing the raw material and getting it ready for dyeing. The loose dehaired cashmere is combed into sliver form, which may seem like a simple step. However, it serves two important purposes: firstly, it makes it easier to process into fine woollen roving during the carding process, and secondly, it allows the slivers to be rolled into balls for the subsequent dyeing stage. By rolling the cashmere slivers into cocoon-like shapes, a hollow centre is formed, making it easier to insert a tube, ensuring more even dyeing in the dye vats. This seemingly insignificant step is, in fact, crucial in maintaining the high standards required in the subsequent stages of production.
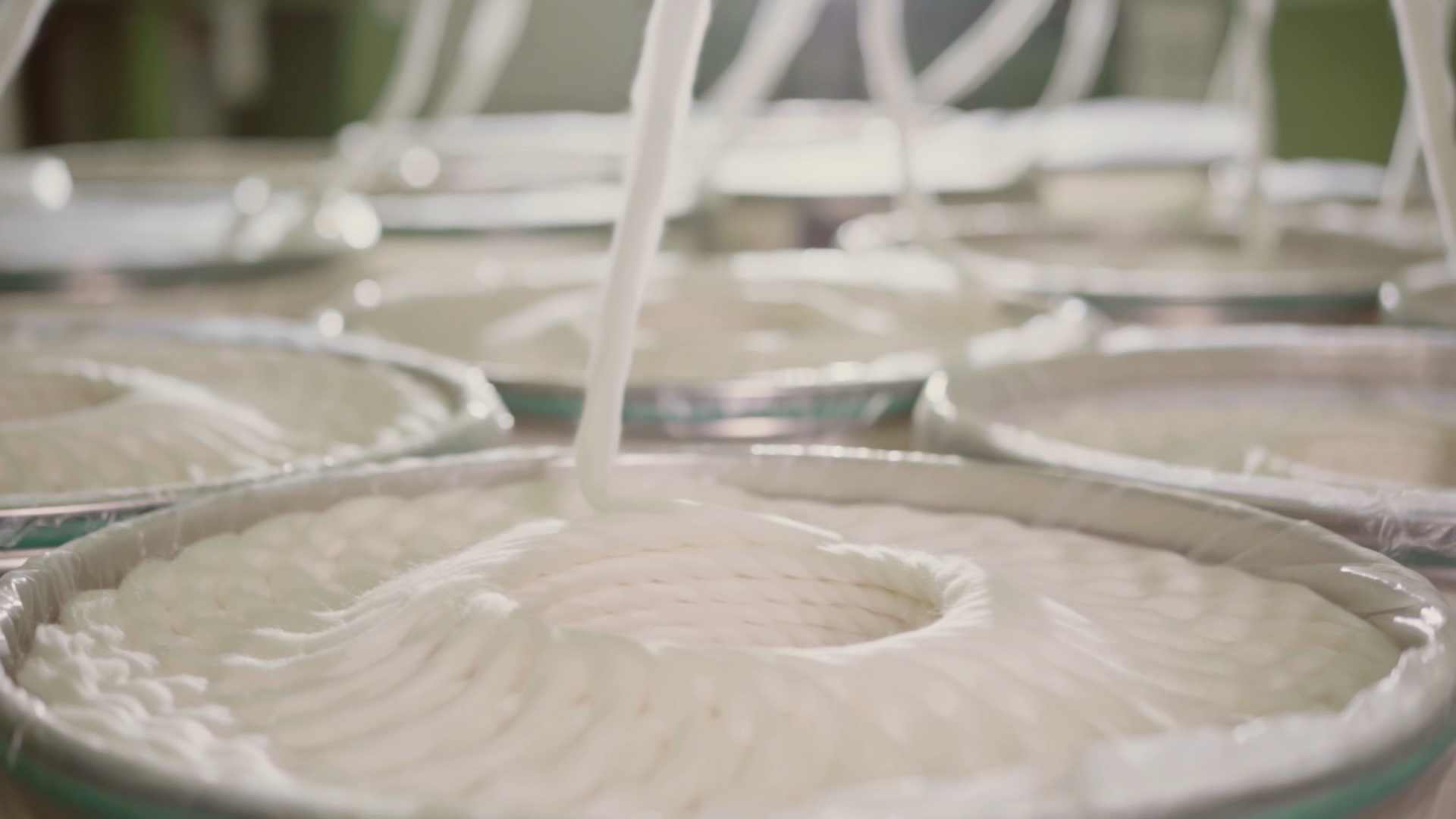
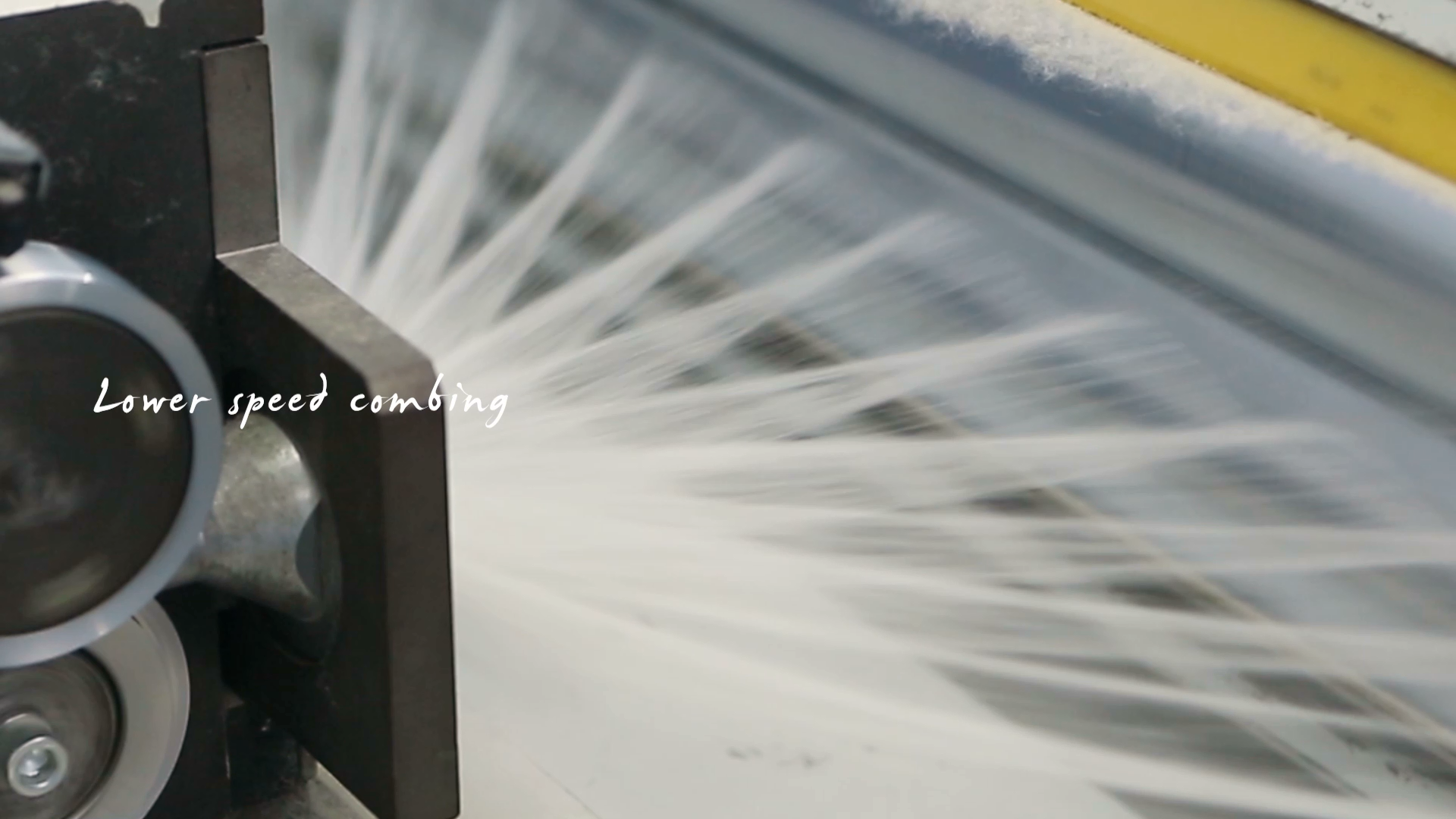
05
High-Count Worsted Spinning
Worsted yarn is produced through a meticulous combing system, which requires exceptionally high-quality raw materials. This process can spin 1 gram of cashmere into 100 metres of ultra-fine yarn, and even up to 120-count yarn. The higher the count, the finer and softer the fibres. With the support of water-soluble fibre blending, it can even reach up to 200 metres of ultra-fine yarn.
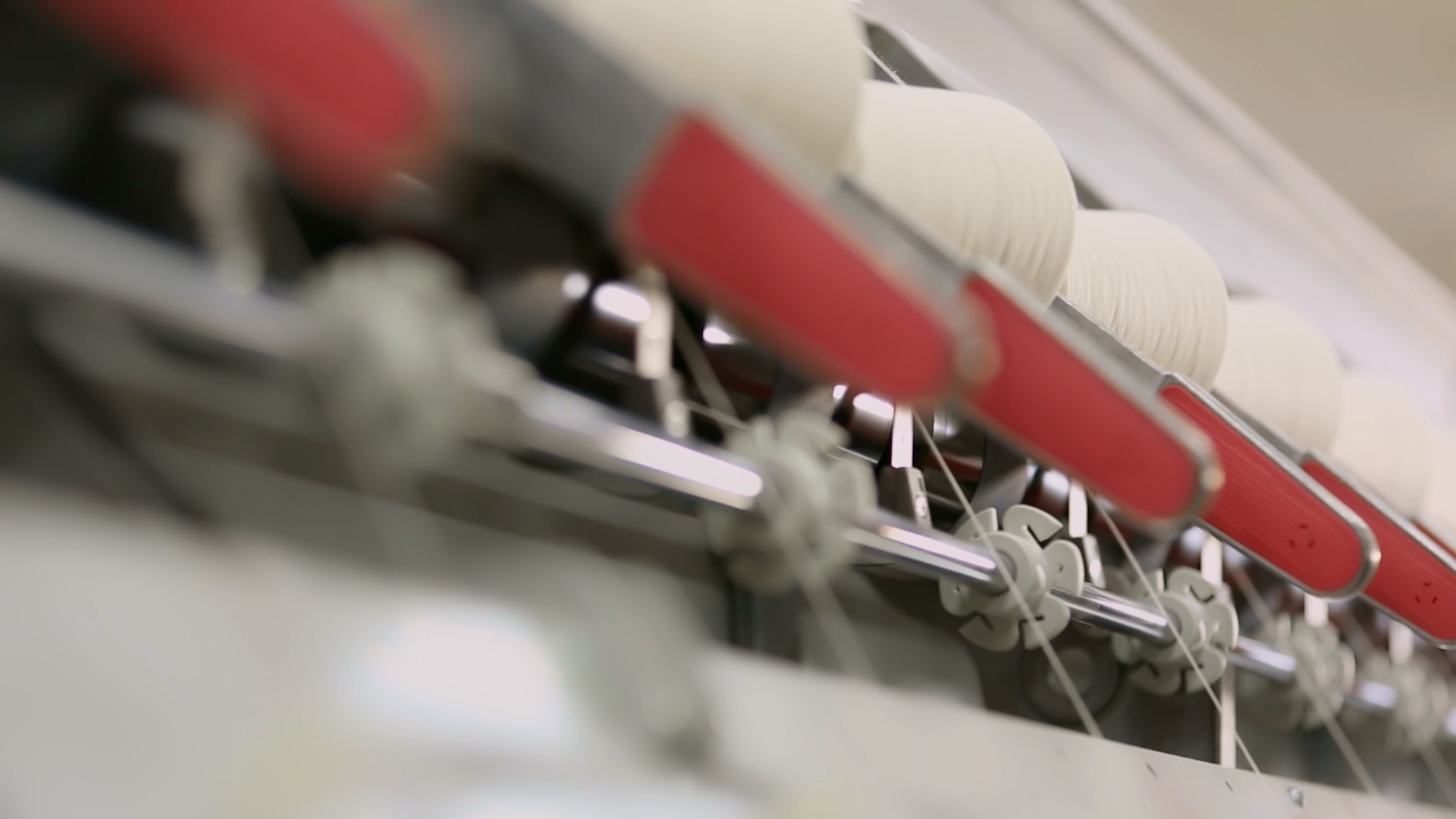
06
Ultra-Worsted Series
The ultra-worsted series is woven from exceptionally fine yarn, with 1 gram of raw material spun into 100 metres of fine yarn. Ultra-worsted cashmere products have a smooth and even surface, with tightly woven, clear textures and a soft, natural lustre.
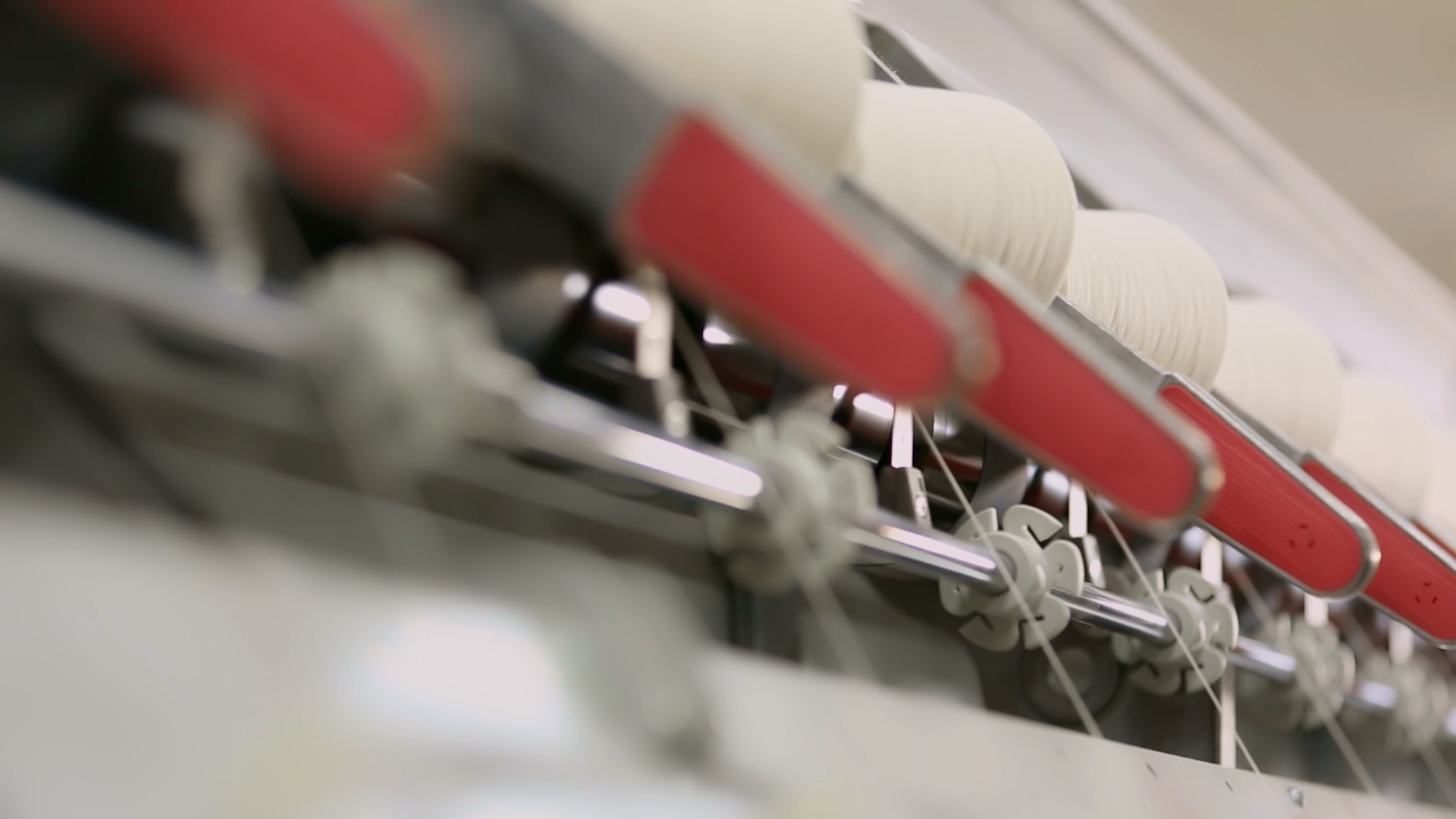
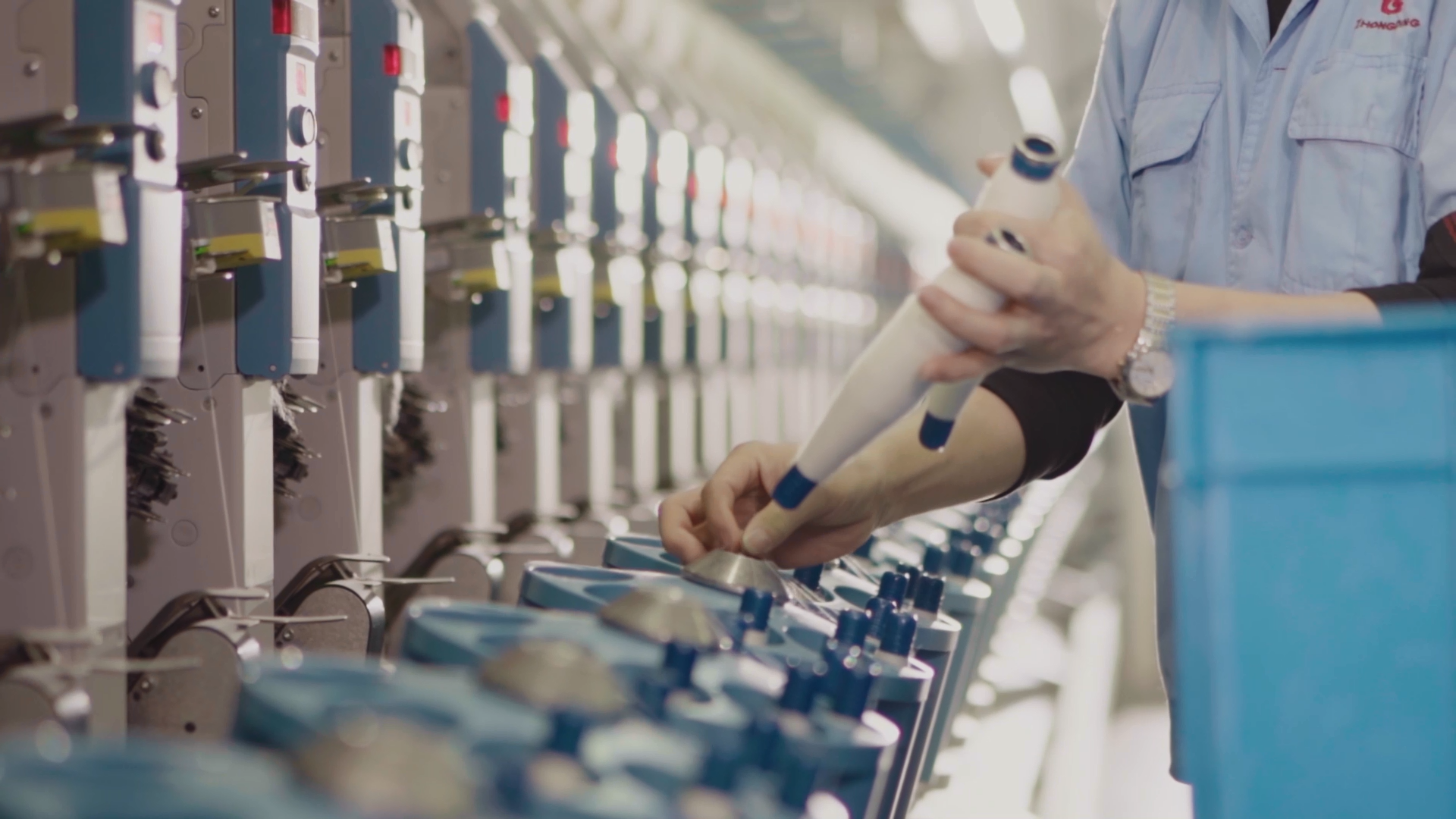
07
Hand Threading the Heddles
This is a painstaking and repetitive process, yet it is this patient effort that creates a flowing beauty akin to performance art. According to the technical arrangement, the warp threads must be threaded through specific heddles, a task that can only be done by hand, as machines are unable to perform it. Simple threading can involve over 5,000 threads in a single day, with each thread needing to pass through the heddles before it can be loaded onto the loom. This step requires the artisan to skilfully weave thousands of threads by hand, with not a single one out of place—any mistake would render the entire fabric defective. The artisan’s fingers move swiftly, as if playing a rapid and powerful piano piece. This beautiful symphony comes from constant practice, and behind the seemingly monotonous repetition lies the dedication of daily persistence and unwavering focus.
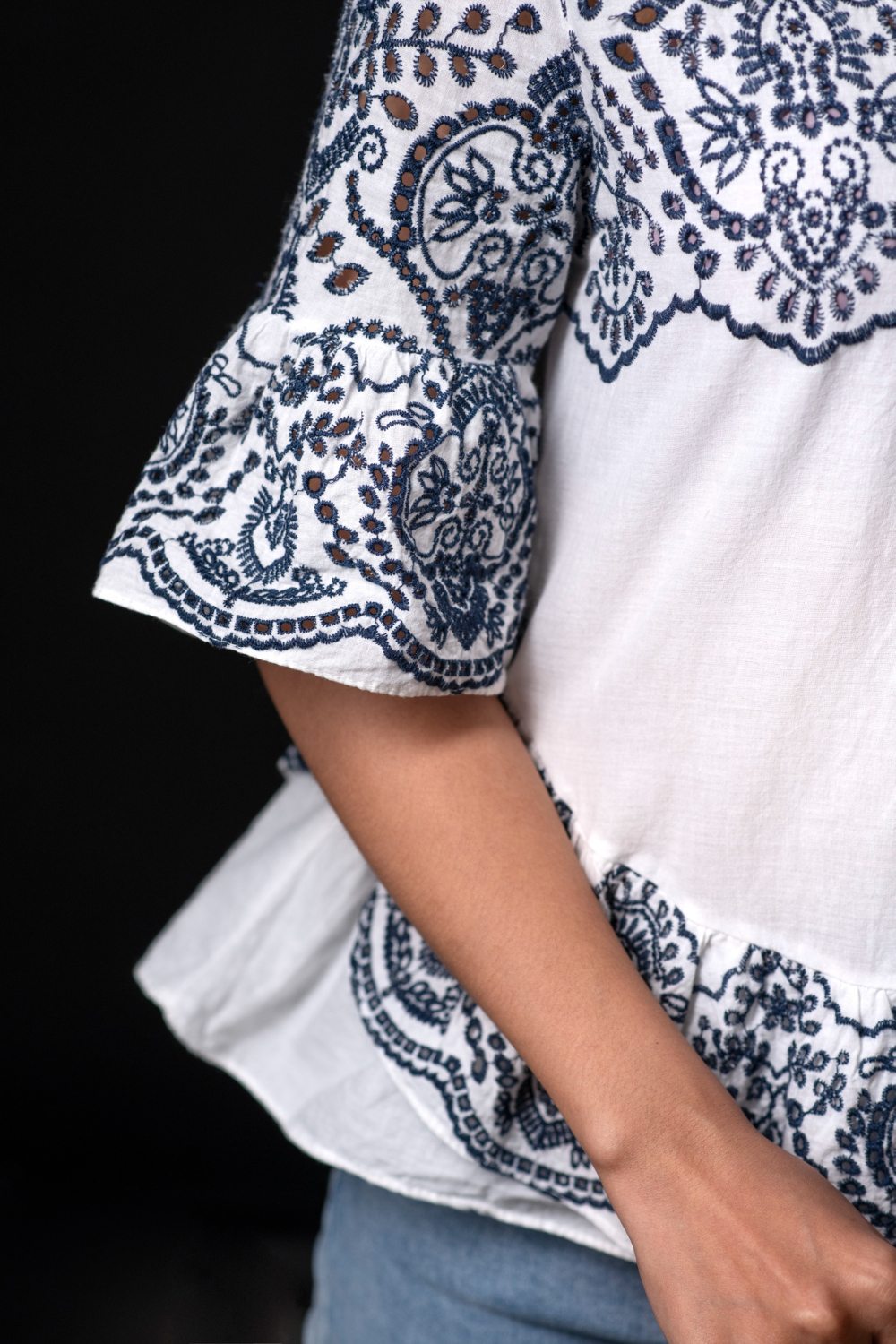
09
Traditional Screen Printing
There is no challenging screen, only meticulous artisans. Screen printing preserves the warmth of handcrafting and embodies a fondness for traditional craftsmanship, giving the printed patterns a more textured, three-dimensional feel. The mesh used to create the screen must be 120 mesh count—the higher the number, the finer the mesh. Before printing, the master carefully checks for any defects outside the intended pattern, using photosensitive glue to block any issues and prevent dye from seeping through during printing. Screen printing is done using a separate screen for each colour. After printing one screen, the next is applied, and for more intricate designs, up to 20 screens may be used.
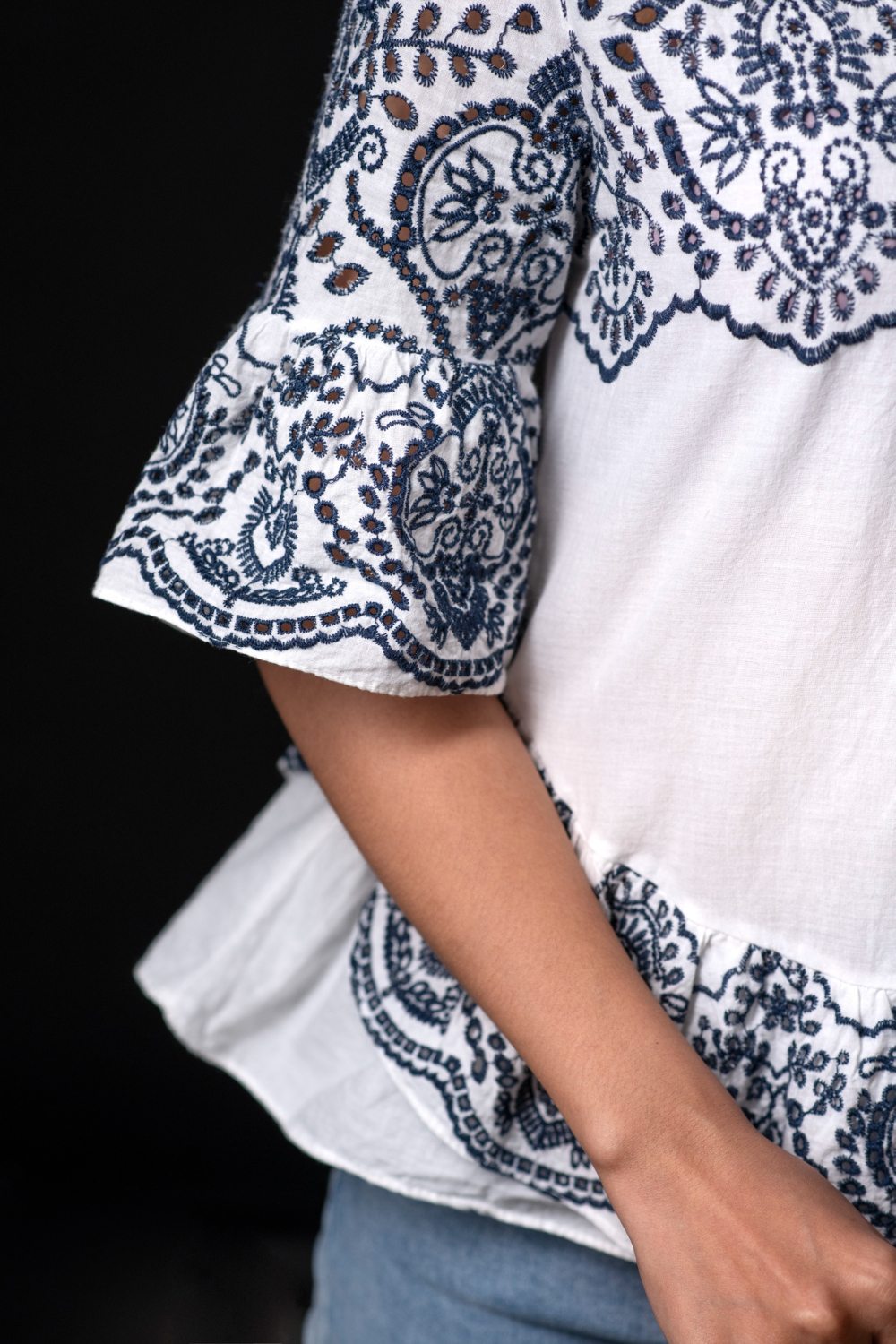
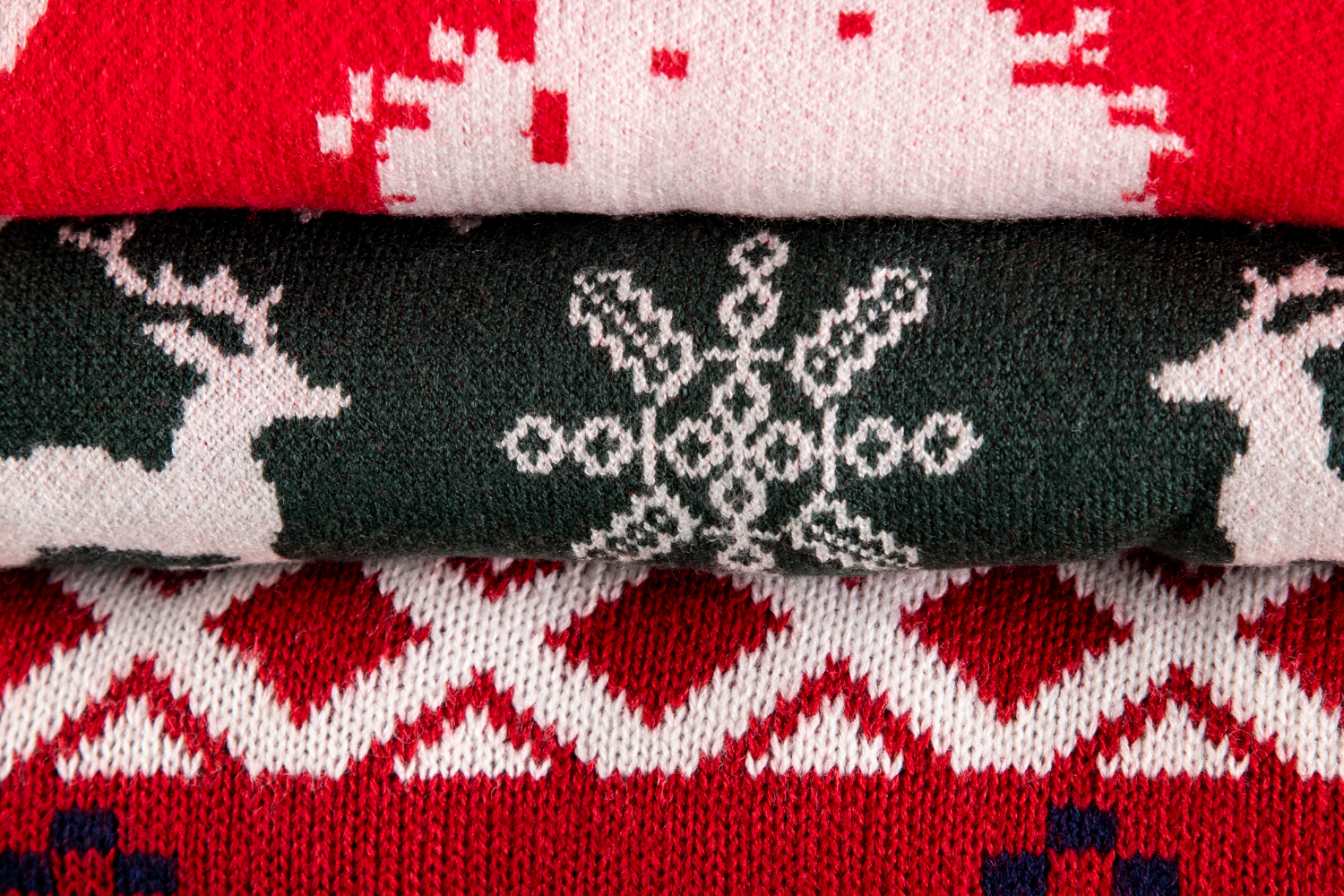
10
Handwoven Jacquard
Due to subtle differences, each garment shines with its own unique brilliance. The slight variations inherent in handcrafting endow each piece with a distinct soul. Master weavers with decades of experience may require several hours to a few weeks to complete a single woven panel, a process that tests their immense patience and focus.
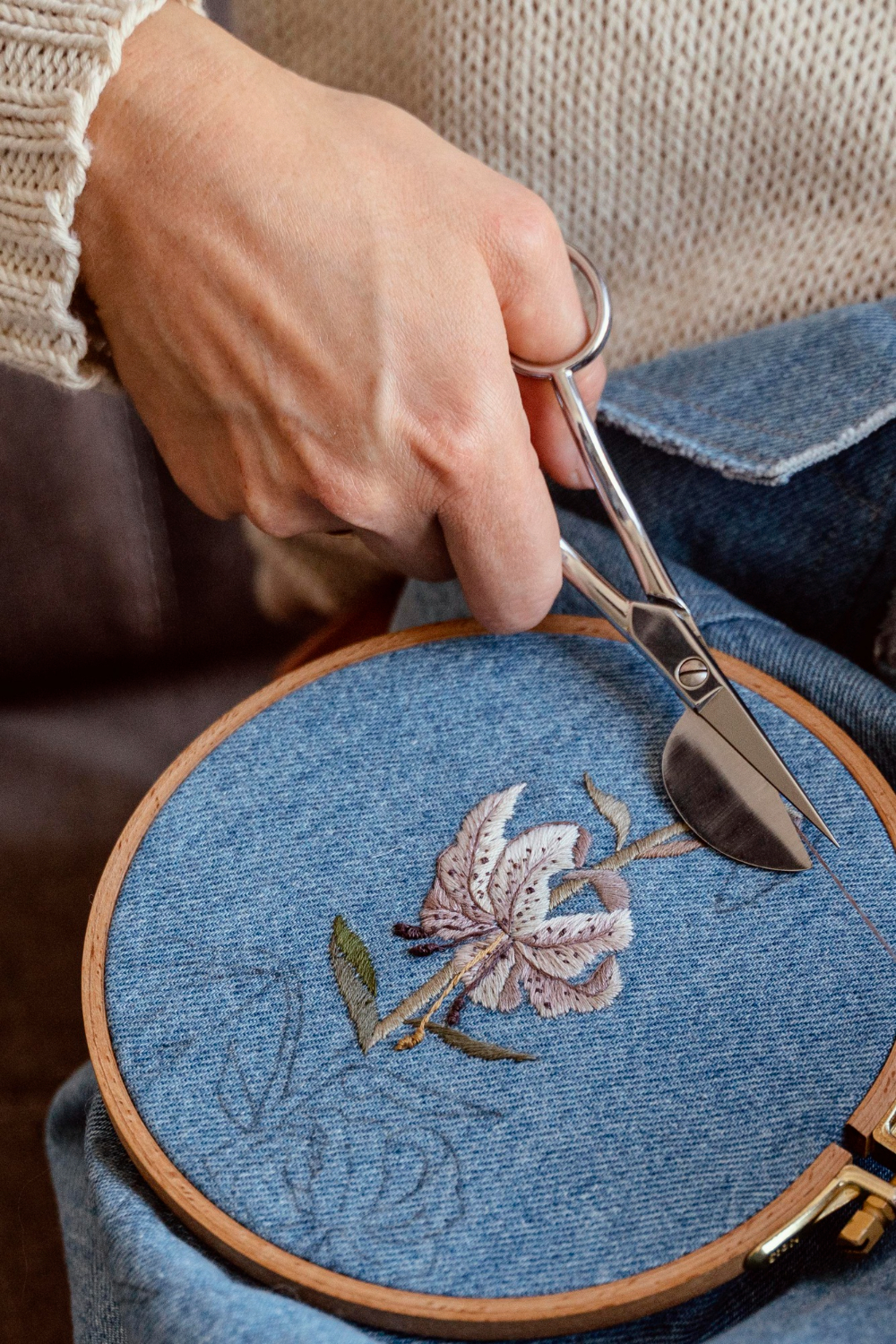
11
Hand Embroidery
The most traditional craft lies in the harmony between handwork and fabric. This delicate and intricate process must be carried out by skilled hand embroiderers, who place a pattern beneath the garment and stitch along the design. Each stitch is made with unwavering focus, and the needle must move in a precise, consistent rhythm to create smooth and even lines. Under the embroidery needle, the threads weave the garment’s timeless beauty, and the warmth of handcrafting brings the patterns to life.
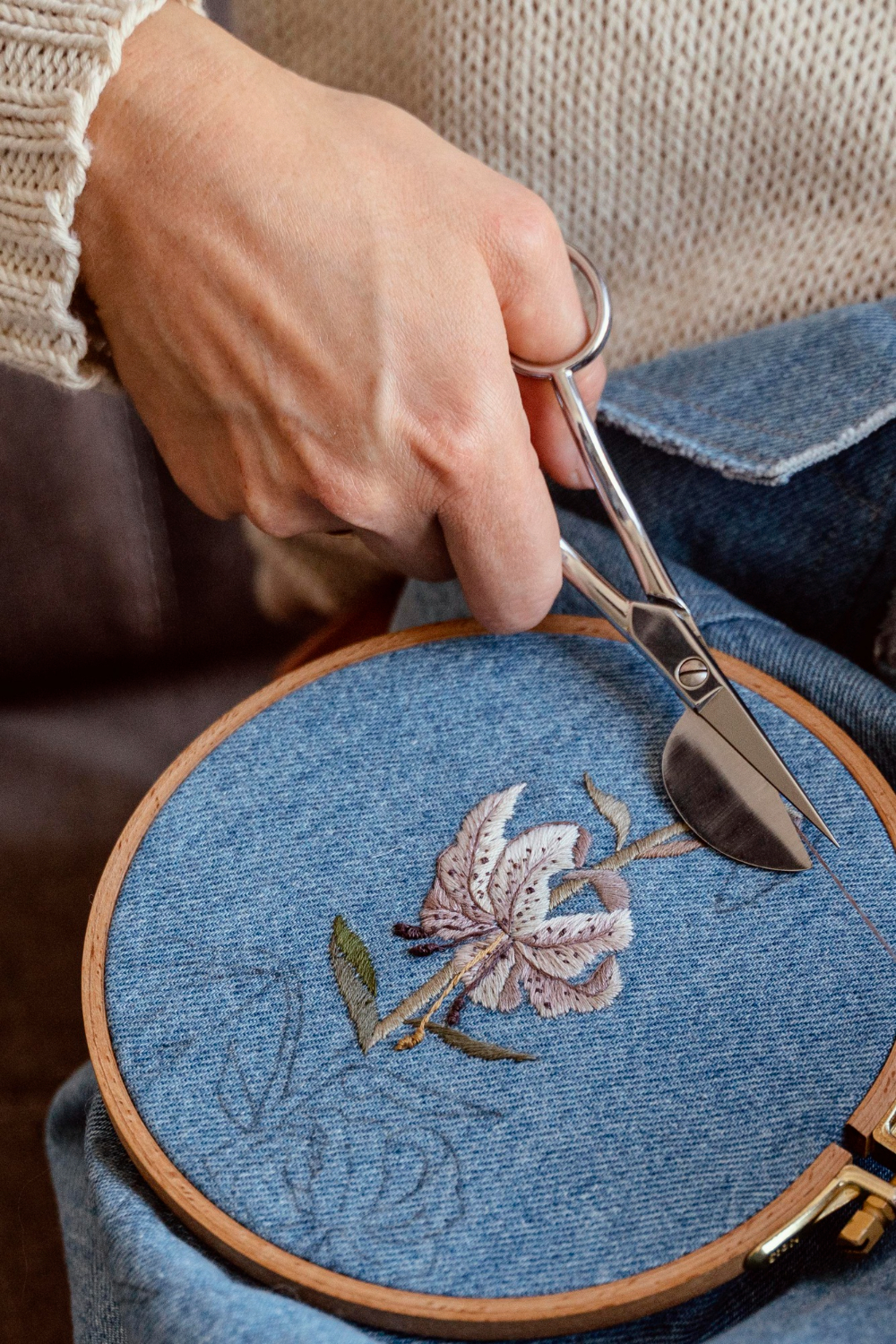